Exploring Top Trends in Industrial Electronic Equipment
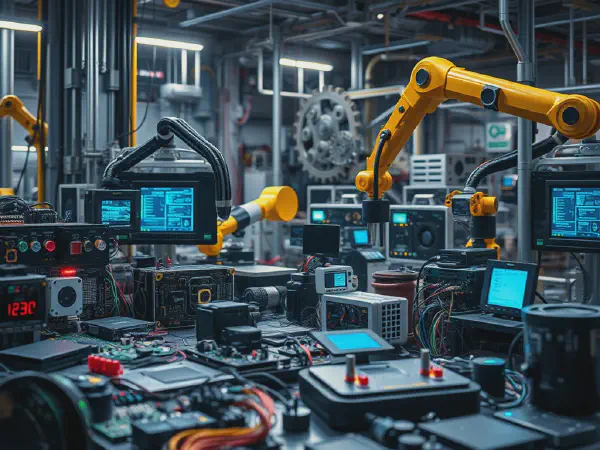
Industrial Electronic Equipment: An Overview
Industrial Electronic Equipment plays a crucial role in modern manufacturing, providing the necessary tools and systems to enhance productivity, efficiency, and safety in various industrial processes. This equipment encompasses a wide range of devices, including controllers, sensors, robots, and communication systems, all designed to automate and improve operations in sectors such as manufacturing, energy, and telecommunications.
As industries continue to evolve, the demand for Industrial Electronic Equipment has surged, leading to innovations in automation technology and system integration. With advanced electronic components, businesses can optimize their production lines, reduce labor costs, and increase product quality. These systems are essential in areas such as process control, data acquisition, and monitoring, enabling real-time decision-making and boosting operational performance.
Finding the best plug in power meter australia can significantly enhance energy management in your home or office.
In summary, Industrial Electronic Equipment is fundamental to the contemporary industrial landscape, providing the backbone for automation in factories and processing plants. Its implementation not only streamlines operations but also contributes to enhanced safety standards, making workplaces more conducive to efficient production. Keeping abreast of the latest trends and technologies in this domain is vital for industry players looking to maintain competitive advantages.
The integration of Industrial Electronic Equipment into manufacturing processes has ushered in a new era of industrial automation. Companies are increasingly investing in these systems to enhance productivity and meet the growing market demands. By leveraging cutting-edge technology, such as IoT sensors and AI-driven analytics, businesses can achieve unprecedented levels of operational efficiency and responsiveness.
A dust resistant keyboard is essential for maintaining performance in dusty environments, ensuring longevity and functionality.
Moreover, the future of Industrial Electronic Equipment is promising, with ongoing advancements in smart technologies, automation, and sustainability driving the industry forward. From energy management systems to quality control applications, the potential of this segment is vast, and companies that embrace these technologies are likely to thrive in the competitive landscape of the industrial sector.
Automation in Industrial Electronic Equipment
Automation is a pivotal aspect of Industrial Electronic Equipment, significantly enhancing the capabilities of modern manufacturing systems. The use of sensors in automation allows for real-time monitoring and control of industrial processes. Sensors collect data on various parameters, such as temperature, pressure, and flow rates, which are then analyzed to optimize operations. This data-driven approach not only improves efficiency but also enhances product quality.
Robotics has become an integral component of manufacturing automation, offering numerous benefits in terms of productivity and precision. By employing robotic systems, industries can perform complex tasks with speed and accuracy, reducing human error and increasing output. Robotics also enables companies to operate 24/7, thus maximizing operational capabilities and driving down production costs.
Investing in a reliable plug in power meter helps monitor energy usage and reduces unexpected electricity costs effectively.
The integration of IoT in industrial automation has transformed how manufacturers operate, providing seamless connectivity and data exchange between devices. With IoT-enabled Industrial Electronic Equipment, businesses can monitor equipment and processes remotely, implement predictive maintenance, and gather valuable insights into operational performance. This connectivity leads to smarter decision-making and the ability to respond swiftly to changes in production demands.
Machine learning is another significant advancement impacting industrial production. By analyzing vast amounts of data collected from various operations, machine learning algorithms can identify patterns and predict equipment failures or maintenance needs. This capability not only minimizes downtime but also enhances production quality by ensuring that machinery operates within optimal parameters.
Looking forward, the future of automated equipment in the industry appears bright. As technology continues to evolve, we can expect further innovations in automation solutions, including advanced robotics, AI integration, and enhanced data analytics. These advancements will empower industries to increase efficiency, reduce costs, and maintain a competitive edge in a rapidly changing market.
Safety Standards in Industrial Electronic Equipment
Safety standards are critical in ensuring that Industrial Electronic Equipment is designed, manufactured, and operated without posing risks to workers or facilities. Regulatory bodies, such as the Occupational Safety and Health Administration (OSHA) and the International Electrotechnical Commission (IEC), establish safety guidelines that must be adhered to by manufacturers and operators alike.
Compliance with safety regulations is paramount in manufacturing environments. It not only helps protect employees from accidents and injuries but also mitigates legal risks and potential financial penalties for companies. Adhering to these standards ensures that equipment operates safely and efficiently, maintaining high product quality while safeguarding human and environmental health.
Electrical safety measures are particularly important when dealing with Industrial Electronic Equipment. Implementing proper insulation, grounding, and circuit protection techniques can prevent electrical hazards that could lead to equipment failure, fire, or injury. Regular maintenance and inspections are essential to ensure these safety measures remain effective throughout the equipment's lifespan.
Moreover, adhering to hazardous location equipment standards is crucial for industries operating in potentially explosive environments. Equipment must be classified and designed to prevent ignition of flammable substances, ensuring manufacturing processes can proceed safely in these challenging conditions. Compliance with these standards greatly reduces accident risks in such locations.
Best practices for safety audits play a vital role in maintaining safety standards in the use of Industrial Electronic Equipment. Regular audits help identify potential safety issues, assess compliance with regulations, and implement corrective measures where necessary. These audits promote a culture of safety, encouraging employees to prioritize safe practices in their daily operations.
Maintenance of Industrial Electronic Equipment
Preventive maintenance techniques are essential for ensuring the longevity and reliability of Industrial Electronic Equipment. Regularly scheduled maintenance activities help identify wear and tear, allowing for timely repairs or replacements before they lead to unexpected equipment failure. This proactive approach not only enhances operational efficiency but also reduces overall maintenance costs.
Common issues with Industrial Electronic Equipment often stem from electrical failures, mechanical breakdowns, or environmental factors. Troubleshooting these issues requires skilled technicians who can diagnose problems accurately and implement effective solutions quickly. Developing a systematic approach to troubleshooting can minimize downtime and keep production running smoothly.
The importance of regular inspections cannot be overstated when it comes to maintaining Industrial Electronic Equipment. Routine inspections help ensure compliance with safety standards and identify potential issues that could escalate into more significant problems. By conducting these inspections consistently, companies can maintain optimal equipment performance and avoid costly delays.
Training staff for equipment maintenance is crucial for ensuring that personnel are well-equipped to handle maintenance tasks effectively. Investing in training programs helps employees understand the equipment better, enabling them to perform routine maintenance and identify potential issues proactively. This knowledge is invaluable in promoting a culture of safety and reliability in the workplace.
Innovative maintenance solutions, such as condition-based and predictive maintenance, are transforming how industries approach equipment care. By leveraging data analytics and IoT technologies, companies can monitor equipment conditions in real-time and predict when maintenance will be required. This proactive approach not only optimizes maintenance schedules but also significantly minimizes equipment downtime.
Applications of Industrial Electronic Equipment
Industrial automation applications represent a significant segment of the Industrial Electronic Equipment market. These applications include robotics, process control systems, and data acquisition systems, all designed to enhance manufacturing efficiencies and streamline production workflows. By automating repetitive tasks, companies can free up human resources for more complex operations while simultaneously improving quality and output.
Energy management systems (EMS) utilize Industrial Electronic Equipment to monitor and control energy consumption within industrial facilities. By implementing EMS, companies can identify inefficiencies, reduce waste, and lower energy costs. These systems also play a critical role in supporting sustainability initiatives by enabling businesses to track their energy usage and carbon footprints accurately.
Telecommunication equipment in industries is another essential application of Industrial Electronic Equipment. Communication systems facilitate seamless interconnectivity among devices and machines, ensuring that data can be shared and processed efficiently. This connectivity is vital for optimizing operations, enabling real-time monitoring, and supporting integrated manufacturing strategies.
Quality control systems leverage advanced Industrial Electronic Equipment to monitor production processes and ensure that products meet strict quality standards. By utilizing sensors and data analytics, these systems can quickly identify defects or variances in products, reducing waste and improving overall manufacturing quality.
Control systems in manufacturing are fundamental to maintaining operational efficiency. These systems utilize Industrial Electronic Equipment to automate processes, monitor conditions, and implement control strategies that optimize production performance. By deploying effective control systems, manufacturers can enhance flexibility, responsiveness, and overall performance.
Future Trends in Industrial Electronic Equipment
Advancements in smart technologies are poised to revolutionize the Industrial Electronic Equipment landscape. The emergence of intelligent systems capable of learning and adapting to dynamic environments will greatly enhance equipment performance, productivity, and operational flexibility. Companies that harness these innovations will position themselves at the forefront of industrial automation.
Sustainable electronic equipment solutions are becoming increasingly important as industries strive to reduce their environmental impact. Manufacturers are focusing on developing energy-efficient technologies and eco-friendly production processes that minimize waste and emissions. This trend is reshaping the market for Industrial Electronic Equipment as companies prioritize sustainability alongside profitability.
The role of AI in industrial sectors is expanding, with machine learning algorithms driving intelligent decision-making and process optimization. AI technologies are being integrated into Industrial Electronic Equipment to analyze vast datasets, predict trends, and streamline operations. This integration will lead to accelerated production timelines and enhanced product quality.
Emerging technologies in manufacturing, such as augmented reality and 5G connectivity, are driving future trends in Industrial Electronic Equipment. These innovations offer unprecedented opportunities for enhancing operational efficiency, enabling real-time monitoring, and facilitating collaborative working environments that enhance productivity across the board.
Finally, global market trends for electronic equipment indicate a significant shift toward digitalization and automation in industrial operations. As businesses adapt to evolving consumer demands and market conditions, the need for advanced Industrial Electronic Equipment will continue to grow, paving the way for innovation and development within the industry.